High-Tech Tools for Network Construction and Maintenance
Everyone loves gear that can help them do their jobs better and save time. No good chef would go into a kitchen without his own knives, while every auto repair location has an OBD2 code scanner close at hand for quickly deciphering the mystery of the infamous “Check Engine” light.
Over the past few years, technologies such as ground penetrating radar (GPR), drones, and LIDAR have been incorporated into the network construction and maintenance toolboxes of contractors and service providers to improve safety, efficiency, and provide more detailed information and documentation on the physical state of outside plant. While these tools and services may have a higher price tag than traditional methods, they typically provide a return on investment through more targeted use of field crews and truck rolls, along with increased worker protection.
Peering Underground
Having a good idea of what is below the surface before the movement of the first shovel or backhoe of dirt is essential in underground network construction, be it a greenfield installation or the need to unearth conduit for repairs or replacement. A locate service is a great first start, assuming buried utilities have metal incorporated into their structures for easy discovery. But there are many situations where more subsurface detail is required, especially in older cities and townships where there are legacy utilities that weren’t designed for ready discovery and historical areas that could hold significant archaeological value and cultural significance.
“For me, one of the biggest issues is trying to figure out where these [underground utility] networks are, as no one has a clue what’s down there in the first place,” said Simon Pedley, Sales Director, Detection, US/Canada for Hexagon Geosystems. “You’ve got an idea where they should be, because that’s what the plans say today. But you’ve also got the 200 years of history that we’ve been burying utility lines, fiber lines, telecom. It’s a difficult world trying to figure out what’s under the ground.”
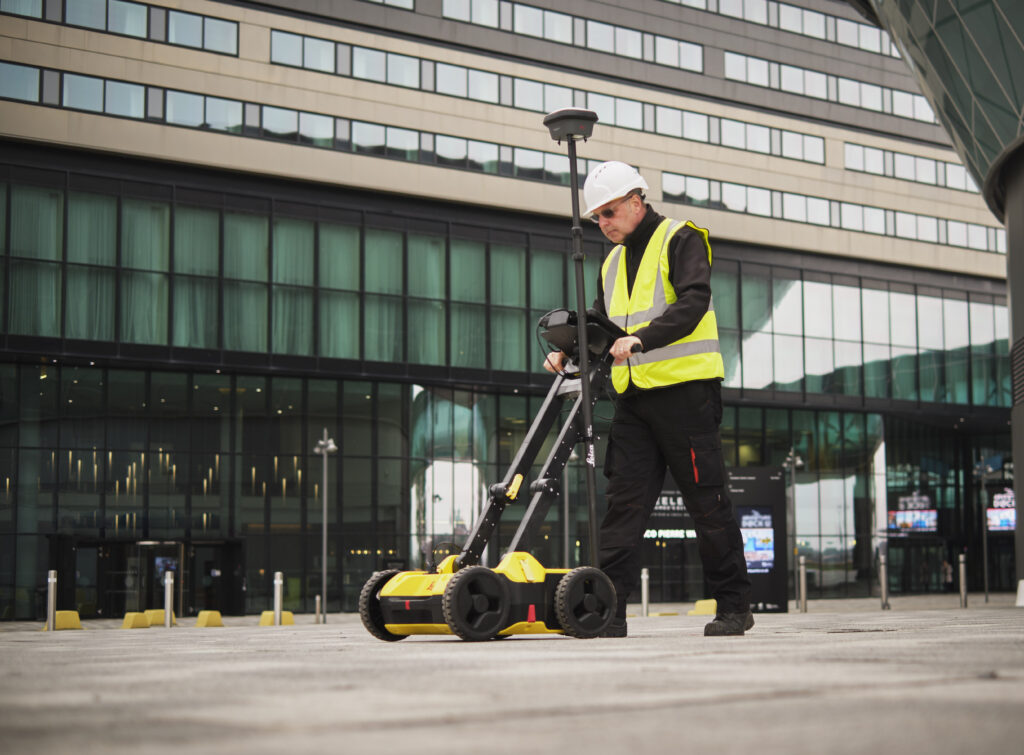
Ground penetrating radar (GPR) can provide a higher level of detail on underground utilities prior to construction, especially for identifying older pipes and lines installed before modern locate requirements. (Source: Hexagon’s Geosystems division)
Ground penetrating radar provides a window into what’s buried below, but it’s not a perfect view by any stretch of the imagination. “In its simplest form, GPR finds material density changes,” said Pedley. “Its greatest asset and biggest Achilles heel is that it finds everything. GPR comes down to the operator of that piece of equipment that needs to pick through and try and determine what’s a line, what isn’t a line. Some of the newer software can help with this interpretation.”
A GPR designed for utility subsurface survey typically looks like a push lawnmower with a tablet at the top of the handlebar, but instead of a motor and a whirling blade there are antennas and electronics, with radio frequency signals sent out, received, and processed into an image. Global positioning system (GPS) information is simultaneously collected to provide location data with the GPR imagery.
Single channel GPRs costing in the range $15,000 to $20,000 provide what Pedley compared to a simple X-ray that can indicate structure and what may be broken, while more sophisticated multi-channel GPRs provide significantly more detail, like an MRI, at a cost of anywhere between $60,000 and $80,000.
“Using multi-channel becomes easier because we have more data, and we work more with a sliced image of an object, like a thermology view, versus a radar gram [blob] where you’re trying to guess is that a pipe, a tin can, whatever,” said Pedley.
Today’s off-the-shelf GPR’s typical view of depth is anywhere from 8 to 10 feet, but performance can vary depending on the type of soil and moisture. Advancements in technology are enabling GPRs to penetrate depths of up to 50 feet, but for most utility applications three to four feet of the surface is sufficient.
Pedley points out that utilities don’t typically take anything out of the ground, with decommissioned pipes abandoned in place next to newer lines. A locate may discover and mark a decommissioned metal gas pipe because the signal is stronger than the newer in-service plastic pipe, and the contractor discovers the difference when they hit the live line.
Given the RF sensitivity of GPR, building an autonomous driving robot around one is challenging and expensive. “The robotic GPR is interesting, but it’s always cost,” said Pedley. “It depends on the workflow. Typically, you’ve got to have someone in the field anyway to interpret the data. It’s quite complex to do just because of the fundamentals of radar to make things purely robotic. When you’ve got motors near radar that are made of metal, you’re going to introduce a lot of noise into the antenna, so there will have to be a lot more shielding. Battery life would be a killer.”
AI and cloud services provide a boost to analyzing GPR data sets, taking collected data and filtering out background noise to present clean information on where utilities are located faster than having humans read and interpret imagery, with the speed advantage increasing with the more data collected.
Pole Flying
Once a novelty, aerial drones are a now a fundamental tool for assessing, documenting, and inventorying above ground assets, including enclosures, poles, and towers. A drone can use its onboard high-resolution cameras to safely visually inspect assets while larger platforms can be equipped with LiDAR laser and thermal heat sensors to provide additional precision and detail for issues such as vegetation management. It can also be utilized to ensure safety prior to field crew operators and provide maintenance recommendations.
Engineering firm PLP has been using off-the-shelf drones since 2016 for surveying and currently operates a fleet of drones for its inspection services. PLP first started using drones to inspect utility transmission and distribution lines and later expanded their offering to broadband providers for their outside plant assets.
A typical drone inspection by PLP will include a field crew with one or more drones and a pair of FAA-certified commercial pilots, one to operate a drone and the other serving as a safety observer. The deployment vehicle will also have extra batteries and a way to recharge them to maximize flight time when conducting a survey. The drone provides still images, video, and location information as it flies up and around the assets being evaluated, providing the advantage that the drone provides a 360-degree view of all the equipment on a pole, as opposed to the more limited perspective from a ground inspection.
“We have an active dashboard we utilize that the drone pilots put their information into, so you’ll have photos, video, location, pole number,” said Dan Levac, Senior New Business Development Manager, PLP. “What that does is provides us with a real time opportunity to share with our customers where we are, what we’re doing and what we’re inspecting. This also permits real time adaptability to change locations so as to not interfere with ongoing construction or maintenance”
The recorded video is also evaluated by a separate analytical team back at the office to evaluate and spot potential problems. PLP uses a color code system inside the dashboard to flag issues discovered during inspection. Green means the asset is good, yellow indicates a potential problem, while red means there’s an immediate issue that needs to be fixed.
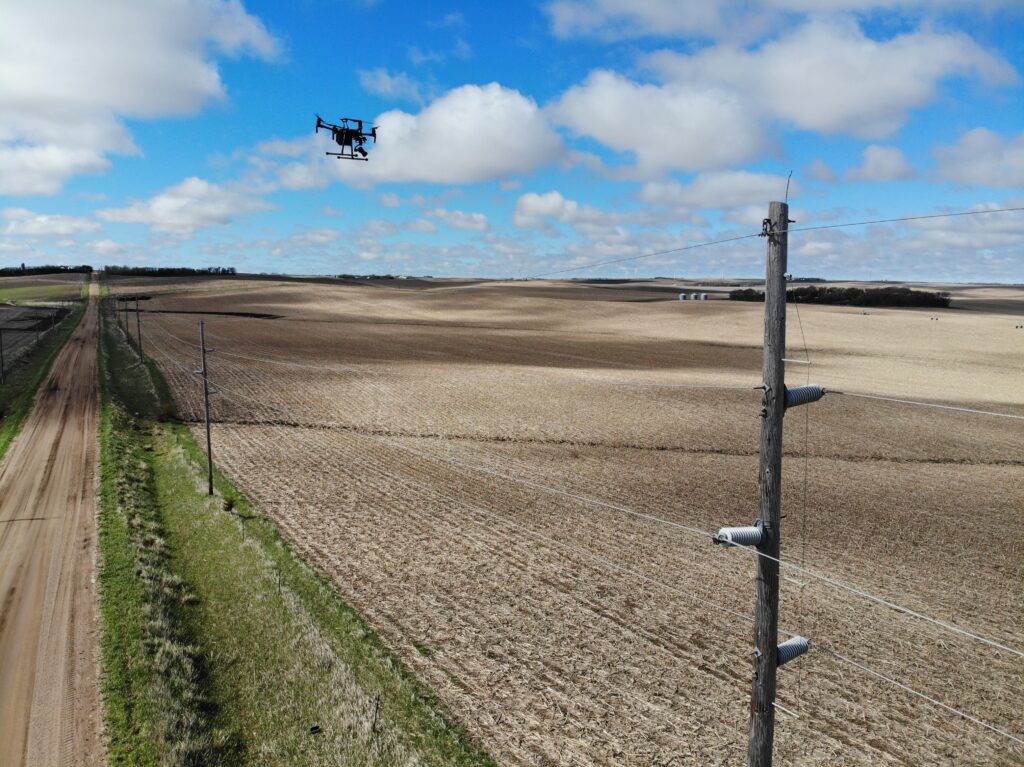
Aerial drones provide both speed and safety when assessing outside plant, especially for remote and more challenging asset locations. (Source: PLP.)
Having a drone conduct the assessment provides enhanced safety in several ways. First, the drone can easily and quickly get to places and locations that would require a ladder or other equipment for setup. In instances where broadband equipment is sharing the pole with electrical services, there’s no risk to field personnel. The availability of stills and video on hand prior to sending out a field crew enables dispatch and repair centers to plan out and walk through repairs and potential safety issues before a ladder or other piece of equipment is placed and a person starts touching assets, so repairs can move more smoothly and quickly once the field crew arrives.
Drones also save time when inspecting poles and lines. There’s a savings of anywhere from 40% to 60% or more of the time it would take for someone to physically walk and potentially climb up for inspection, with additional accuracy and certainty provided through the secondary back-office review of imagery.
“There’s a lot of time savings that come from the fact that if you’re a drone operator you don’t have to go to every single pole in person,” said Craig Baldwin, Technical Sales Manager and the “Drone Guy” at PLP. “You can just hop from one pole the next. Flying the drone also gives you the ability to get to those poles up on hills, across valleys, or just inaccessible. They can just fly up and avoid obstacles if necessary.”
Like their human counterparts, working in inclement weather can impede the effectiveness of drone operations. “The drones generally don’t care, but you certainly have to think about the data you are collecting,” said Baldwin. “If it is raining, the drone might not fall out of the sky, but you might get mist or droplets of water on the camera, which makes the images worse. Generally speaking, we like to avoid inclement weather, but if something comes in on the crews when they’re out doing the work, there’s no worry about the drone failing just because it got wet.”
Additional sensor payloads come into play depending on the customer, with power customers desiring thermal imagery while LiDAR is used to create a 3D map in and around assets to identify vegetation problems that need to be remedied by field crews to trim tree branches and other overgrowth that could cause a problem with lines. LiDAR can also provide documentation for make-ready surveys and builds when third parties want to use poles.
“We’re generally capturing five to 10 gigabytes worth of data on a given [visual] inspection,” said Baldwin. “I forget how many terabytes that we’ve collected over the past five or six years. It’s a lot to the consternation of our IT department, because we do a lot of this archiving internally.” An older project using a 20-megapixel camera-equipped drone that surveyed 2,100 rural poles over 156 miles collected 52,000 images amounting to 300 Gb of storage. For more detail and faster surveying, drones can be equipped with an off-the-shelf higher resolution 100-megapixel camera.
Baldwin has found that asset owners he’s talked to are adopting drones for use by their own field crews for repairs and inspection. “They’ll have people out doing their normal work and if they need to get a closer look, instead of climbing or firing up the bucket, they’ll toss the drone up there and have a look. From an image gathering standpoint, that’s as good as being on a bucket truck and doing it by eyesight.”